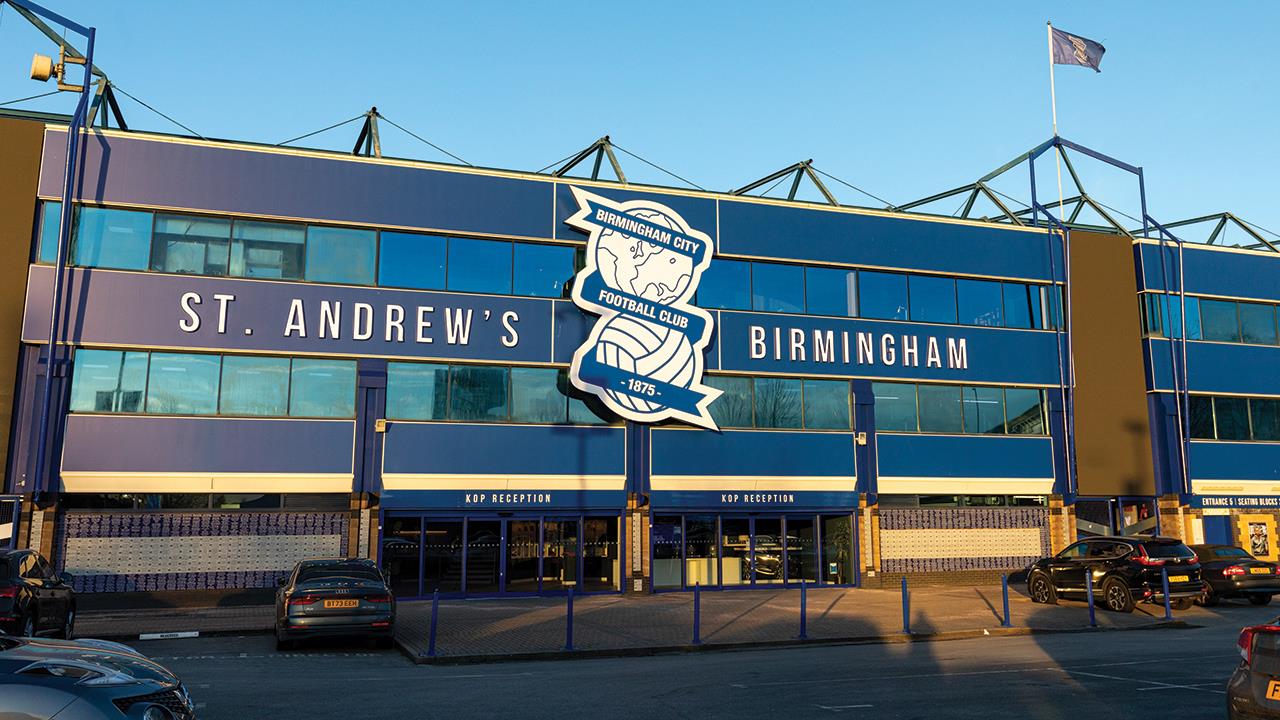
It is well established that a reliable, efficient heating and hot water system is central to delivering high comfort levels for building occupants and optimal energy performance. This, in turn, can help avoid unnecessarily high energy bills and associated carbon emissions.
Certainly, for a football club like Birmingham City (BCFC), ensuring optimal comfort is a key priority throughout its stadium and training facilities. When the decision was taken to refurbish the main Kop plant room at St. Andrews stadium, specialist mechanical service and maintenance contractor Ignis Group was appointed to design and install the new system.
The plant room serves BCFC’s hospitality suites, Legends’ Lounge, and catering kitchens, making reliability, improved efficiency, and quality top of the club’s list of requirements. Space constraints within the plant room were an added consideration for Ignis Group when proposing replacement boilers and water heaters.
Selection criteria
When it comes to product selection, quality and longevity typically top the list of criteria. But reliability, ease of installation, maintenance, and servicing, as well as availability of part replacements, are additional factors that should also influence choice.
This is embodied in the 10-80-10 rule which outlines the total lifetime costs of a commercial building. While 10% of those costs is invested at the construction stage and a further 10% on the building’s demolition, 80% is spent on its maintenance and operation. Taking a whole-life costing approach that includes ease of maintenance is therefore key if the plant is to continue to operate efficiently throughout the building’s lifecycle.
Ease of control is a further element that should be considered at the outset. According to the Carbon Trust, inadequate or incorrect application of a boiler control can add more than 15% to energy consumption (and associated costs), compared to a well-controlled system.
Best solutions for BCFC
As renewable technologies were not considered viable on this project, Ignis Group recommended installing Remeha and Andrews Water Heaters products as the best solution. Remeha and Andrews Water Heaters are part of the Baxi Group.
Ignis Group Director John Mackin explained: “We are very familiar with Remeha products, having used them extensively over the years and been impressed with their proven high performance, energy efficiency, and reliability.
“To meet the heating demand within the space limitations, we proposed installing three Remeha Quinta Ace 90 boilers on a Remeha cascade system.”
With high efficiencies, low Class 6 level NOx, and advanced controls, the Quinta Ace range has been designed for straightforward installation and trouble-free operation.
Backed with seven year warranty, it offers peace of mind of reliable ongoing performance to both installer and end-user. The optional cascade system provides a flexible, easy to assemble solution, reducing labour costs and time, as well as on-site hot works.
John continued: “For the washrooms and kitchens in the hospitality area, which have high hot water demand, we recommended two Andrews ECOflo condensing water heaters due to their high efficiency and reduced maintenance. Baxi being a local supplier was an added advantage to reduce the environmental footprint of the project.”
The ECOflo offers excellent hot water recovery, energy efficiency, and low NOx to satisfy the demands at St. Andrews. The Vitrasglas-lined, thermally efficient tank is protected with maintenance-free, factory-fitted Correx anodes, and equipped with a Hydrojet sediment reduction system.
This, together with the Microban antimicrobial product protection that prevents the growth of bacteria, mould, and mildew on the surface of the tank lining, enhances the performance and prolongs the life of the product.
With the specification approved, a temporary plant was installed in the Kop plant room to maintain continuity of service while the works took place.
Manufacturer support
Baxi provided support throughout the project, from pre-sales discussions to the final commissioning of the new system.
Early engagement with manufacturers can bring multiple benefits to a project. First, many manufacturers will accompany you on free site surveys to understand the project requirements and limitations, and propose the most appropriate solutions. This can be a great opportunity to tap into their specialist product and technical knowledge.
They can also offer specific advice on how to optimise whole-life boiler performance on a particular project – from water treatment and hydraulic separation, to controls and system design.
Manufacturers being able to supply complete heating and hot water solutions also helps simplify the delivery process.
When working on projects with tight timeframes, as was the case at BCFC, a conversation at the outset to check product availability can also be helpful, as John explained: “This project needed to be completed within a fixed four-week period, so the ready availability of the Baxi products was a major bonus, helping keep the job on schedule.”
Moving from non-condensing to condensing technology adds new flueing requirements, which, in this instance, were met by flue specialists Midtherm Flue Systems.
The project also involved the fitting of new pipework, as well as the development of a new controls philosophy to ensure maximum efficiency from the new Remeha boilers and Andrews Water Heaters. All products were supplied through local merchant P & R Edmonds.
John summed up his experience: “It went brilliantly. We had great support from the Baxi technical sales team – they really know their stuff and are always great to use as a sounding board. Their engineers are very competent too and did a great job at the commissioning stage.”
Efficiency savings
With the project now successfully completed on schedule, BCFC is delighted with the result. Ignis estimate that the old system had been operating at a seasonal efficiency of around 65-70%.
With the upgrade to more energy-efficient condensing boilers and water heaters, the club stands to reduce energy consumption from heat by about 20%. Added to this is the improved overall efficiency of the building, the reliability of the service, and the enhanced comfort levels for the club’s hospitality guests.
Small steps, big changes
Ultimately, the goal is to decarbonise heat in buildings. But, irrespective of the heating technology that may eventually be used in a building, energy efficiency is a crucial factor at any time – and that applies especially to heating and hot water systems, which are typically large users of energy.
In plant rooms where renewable technologies are not a feasible option, refurbishing these vital services with a plant upgrade can therefore be a practical step to improve system efficiency.
In line with Building Regulations, the system’s distribution pipework and heat emitters should also be reviewed and upgraded to allow the system to operate more efficiently at a maximum flow temperature of 55°C or lower.
Such future-proofing will, in turn, prepare the heating system for a successful integration of low-carbon technologies, which operate most efficiently with low temperature outputs.
In summary, this project illustrates how achievable early steps can prepare the pathway to longer-term sustainability goals, all the while making operational efficiency savings.
And that’s surely a win-win.
If you'd like to keep up-to-date with the latest developments in the heating and plumbing industry, why not subscribe to our weekly newsletters? Just click the button below and you can ensure all the latest industry news and new product information lands in your inbox every week.